Sustainability
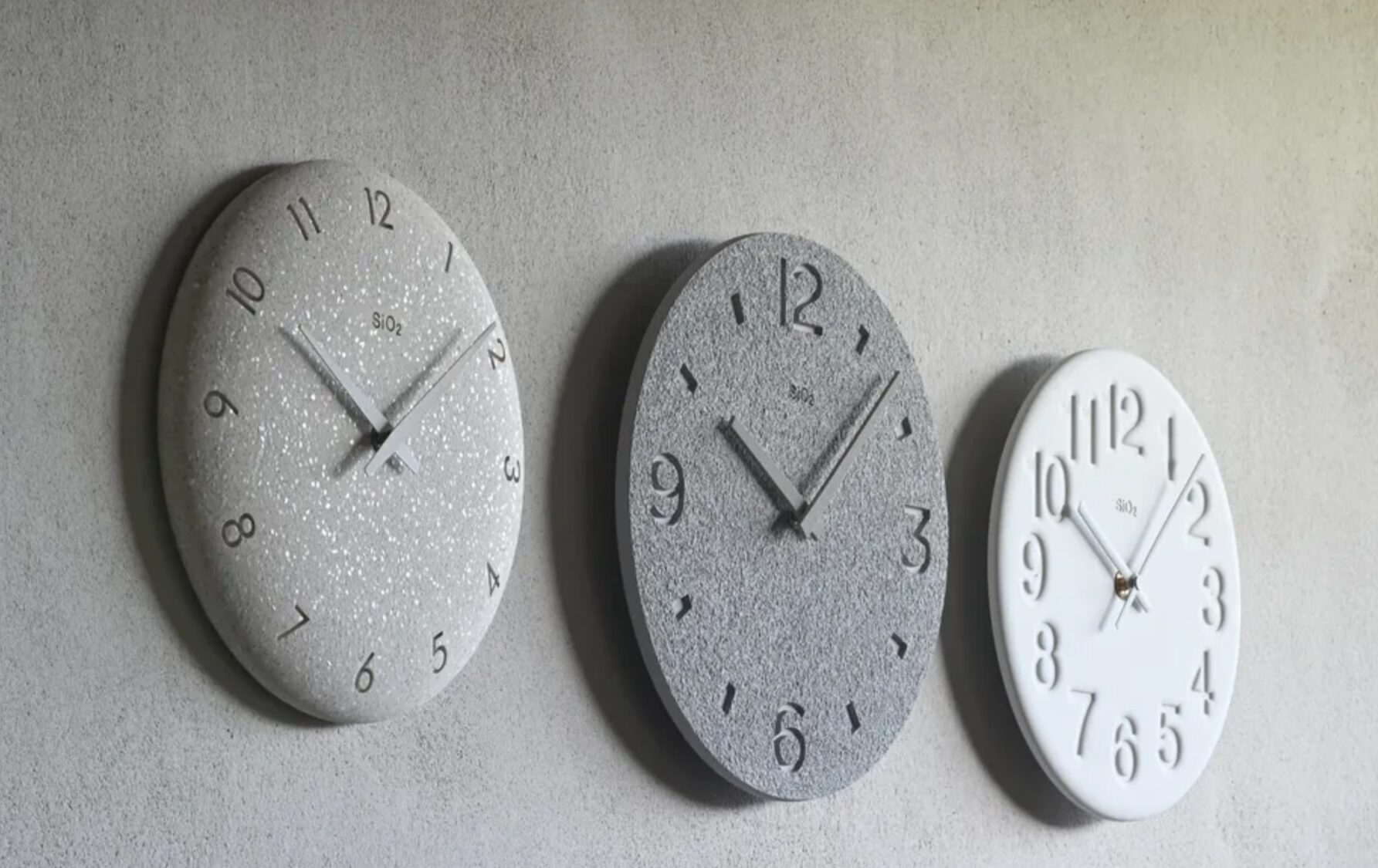
Lemnos Sustainability 10
SiO2 Clock – Craftsmanship Utilizing Local Materials and Techniques
This series of wall clocks was born from the encounter between diatomaceous earth nurtured in the Noto Peninsula, a designer living in Noto, and plastering artisans from Kanazawa.
Two Distinct Challenges Addressed: “Diatomaceous Earth Waste” and “Fear for Diminishing Plastering Techniques”
In 2010, when this project was first developed, Lemnos was exploring ways to utilize local materials and techniques while adopting eco-friendly production methods. The Noto Peninsula, where the designer resides, is rich in diatomaceous earth, a sedimentary deposit formed from the accumulation of phytoplankton on the seabed over time. This natural resource has long been used for products such as bricks and stoves.
However, a significant amount of diatomaceous earth was left unused during the production process, leading to waste disposal issues. In Kanazawa, a historic castle town within the same prefecture, many traditional “machiya” townhouses remain. These buildings have long relied on plastering techniques to create earthen walls. In recent years, however, opportunities to apply these techniques have decreased, leading to a shortage of skilled craftsmen and concerns about the preservation of these traditional techniques.
By combining diatomaceous earth with plastering techniques, we sought to explore new ways to repurpose this material into clocks while also creating opportunities for the preservation and transmission of these techniques. The reuse of waste materials and the use of plastering techniques for molding eliminate the need for heat energy during firing, making this an eco-friendly manufacturing process.
Noto Peninsula: layers of diatomaceous earth formed by the accumulation of marine phytoplankton
A New Expression Realized Through the Characteristics of Diatomaceous Earth and Adapted Plastering Techniques
Diatomaceous earth is a fine-grained material with a soft, smooth texture. It molds easily, delicately capturing details and expressions. By combining these material properties with the craftsmanship of Kanazawa artisans, who have over 100 years of experience in plastering traditional architectural structures, we explored designs that ensure excellent readability while blending seamlessly with modern interiors.
To achieve smooth textures and precise clock shapes, we used silicone molds and created clock bodies with minimal distortion and shrinkage. We designed three-dimensional dials and original markers tailored to plastering techniques, incorporating varying shadow effects to enhance readability and give the clock a fresh, innovative look.
Moving beyond the traditional role of plastering in wall finishes, skilled artisans took on the challenge of applying their techniques to product manufacturing. This effort resulted in the creation of diatomaceous earth clocks that harmonize with contemporary spaces like never before. By showcasing the potential of diatomaceous earth and plastering techniques, we have developed this clock series, which has continued to evolve for over 10 years.
SiO2 Clock (Designed by Yuichi Nara)
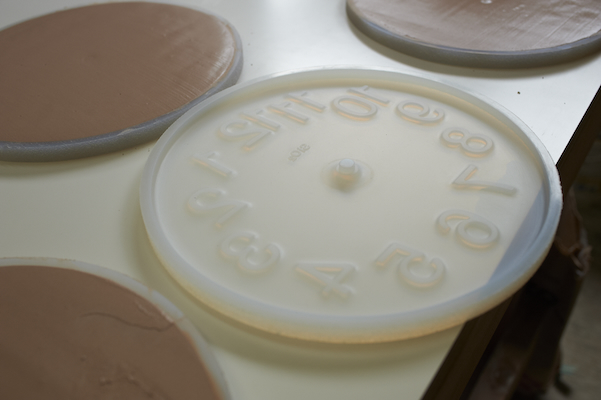
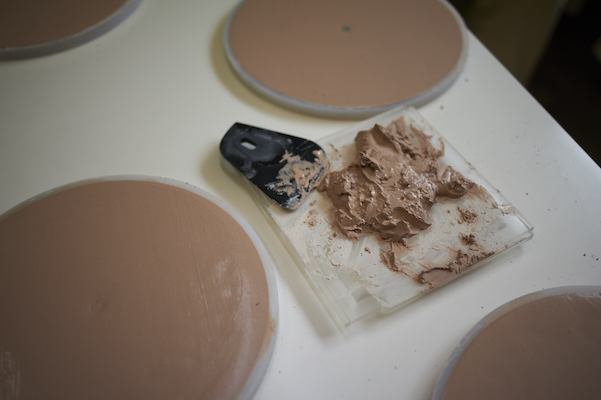
(Left) A silicone mold is used to achieve the smooth texture of diatomaceous earth.
(Right) The mold is carefully filled to prevent air bubbles.
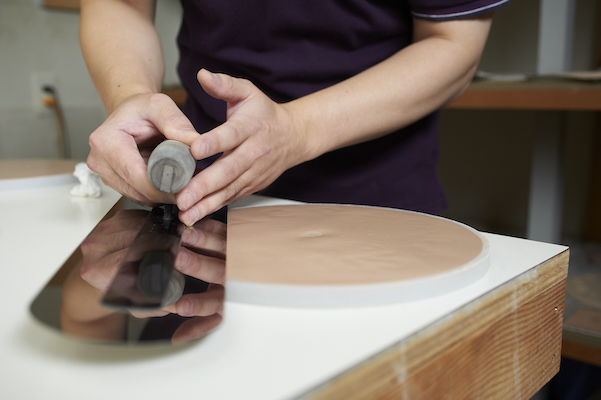
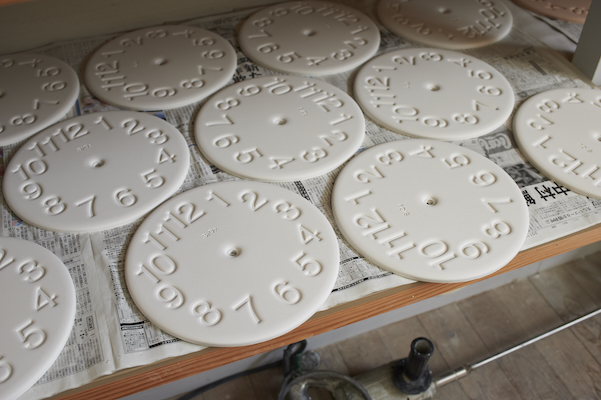
(Left) A trowel is used to smooth the back surface, which will rest against the wall.
(Right) The clock body is left to dry completely.
Three Face Designs, Each with a Distinct Character
The first design retained the natural color of diatomaceous earth to highlight its soft and gentle texture. The rounded surface and embossed numbers emphasized the material’s inherent beauty.
The second design employed the “Kakiotoshi” plastering technique, introducing a rough texture with fine irregularities on the surface of the clock face. To complement the unique texture, we crafted the clock hands using a 3D printer for the first time, adding depth and dimension—an innovative fusion of traditional craftsmanship and modern technology.
The third design employed the “Arai-dashi” technique, embedding natural stones—an element of contrasting material— across the entire surface to create a thicker, three-dimensional face. Its gently curving shape creates a gradient of light and shadow, emphasizing the rich textures of the embedded stones. By molding without tapering, the sharp edges of the carved numbers contrast with the stone finish, enhancing readability through light and shadow.
Beyond merely showcasing the material itself, the addition of skilled plastering techniques has resulted in clocks with diverse textures and a distinct presence.
SiO2 Clock: “Kakiotoshi”
This technique involves scraping the surface before it fully dries using brushes or trowels, intentionally creating fine irregularities to add texture and character.
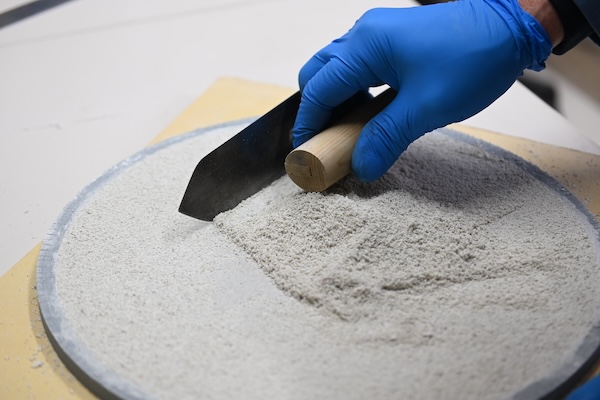
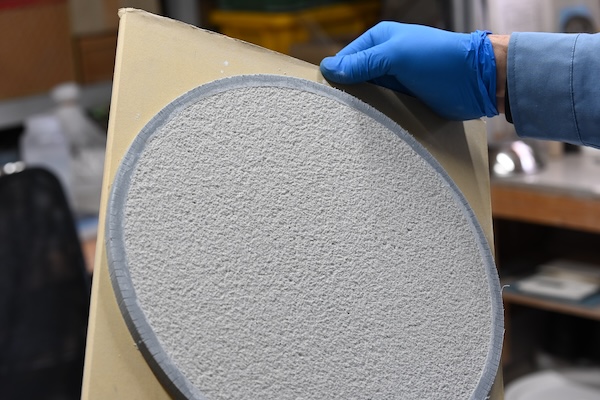
Hardened diatomaceous earth is scraped off with the edge of a trowel.
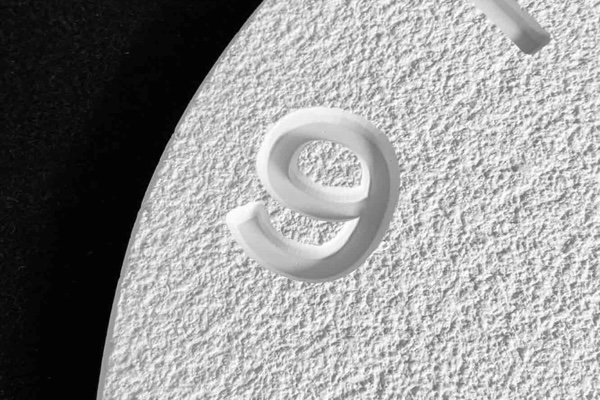
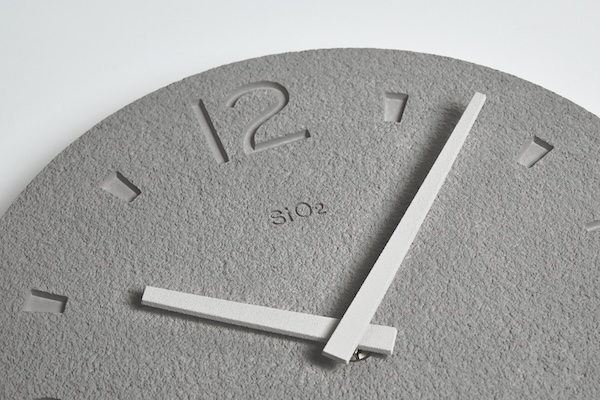
(Left) A rough-textured surface with smooth-edged, carved numbers.
(Right) The clock hands are produced using a 3D printer for the first time, merging traditional craftsmanship with modern technology. SiO2 Clock: “Arai-dashi”
This technique involves mixing stones or sand into the mortar base. Before it hardens completely, the surface is washed and brushed to remove the outer layer, exposing the embedded materials and creating unique patterns.
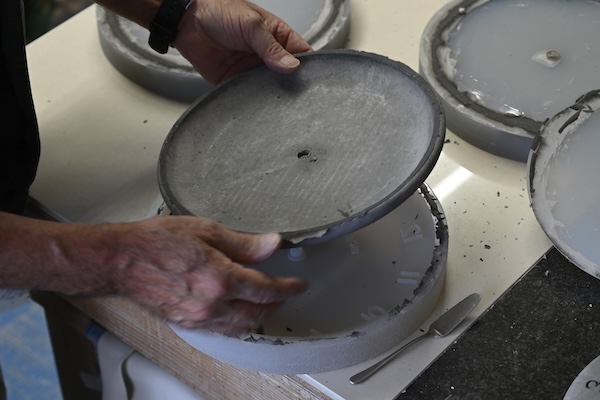
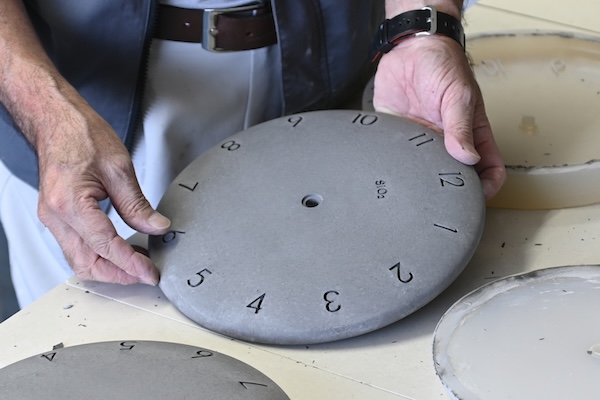
(Left) The dial is carefully removed from a complex mold that also includes a mold for the back panel.
(Right) The numbers on the dial are engraved with a draft angle that cannot be achieved with plastic molding, highlighting the sharpness of the edges.
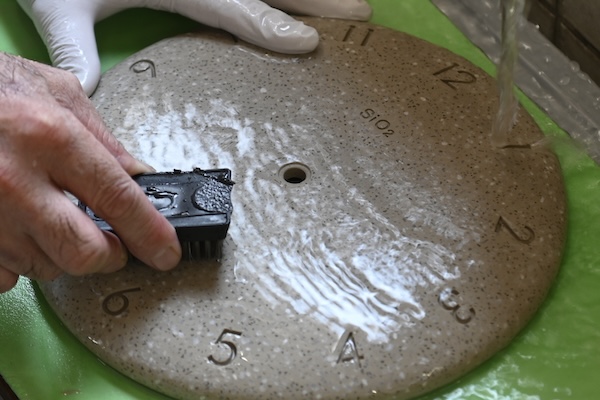
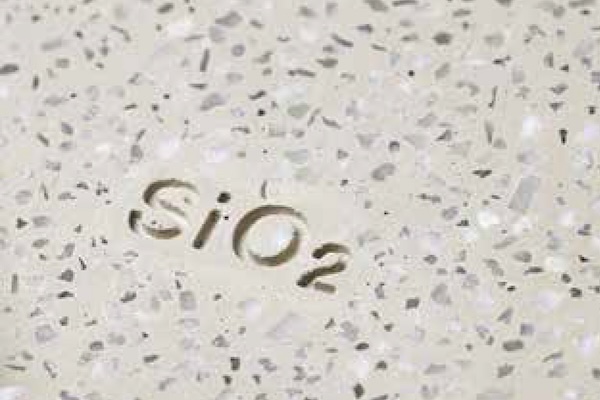
(Left) The surface is washed with a brass brush to reveal embedded stones.
(Right) The clock uses pure white crystalline stones called Kansui-seki as aggregates. Up close, countless uniquely shaped stones reflect light and create a sparkling effect. The element symbol “SiO₂” represents silica, the main component of diatomaceous earth.
From Noto to the World – Contributing to the Preservation of Craftsmanship
The development of diatomaceous earth clocks began in 2010, with the first release in 2011. Over the past decade, three distinct designs have been launched, and approximately 20,000 units have been sold to date. Available at many design shops across Japan, the clocks have now expanded into international markets. They received the Golden Pin Design Award (Taiwan) in 2016 and the Good Design Award 2024 this year.
Despite being part of the well-established category of wall clocks, these products function as a medium to showcase traditional materials and techniques. They have been embraced by people worldwide as part of daily life. Locally, in Ishikawa Prefecture, where the clocks are manufactured, this project has opened up new applications for diatomaceous earth and plastering techniques beyond their traditional construction uses, contributing to the preservation of craftsmanship.
With a desire to promote diatomaceous earth, abundant in the Noto region, where the designer resides, the clocks feature the “SiO₂” logo, symbolizing silica, as a unifying element. Earlier this year, the Noto Peninsula Earthquake caused large-scale upheavals and landslides, exposing rich diatomaceous earth deposits across the region. The earthquake has raised concerns about the survival of local industries that have long relied on diatomaceous earth. In this context, we remain committed to promoting the Diatomaceous Earth Clock as an accessible product that highlights the beauty and potential of this material, while supporting the preservation and revitalization of these industries.
(Left) Takata Lemnos Executive Director Kikuchi, (Right) Designer Yuichi Nara