Sustainability
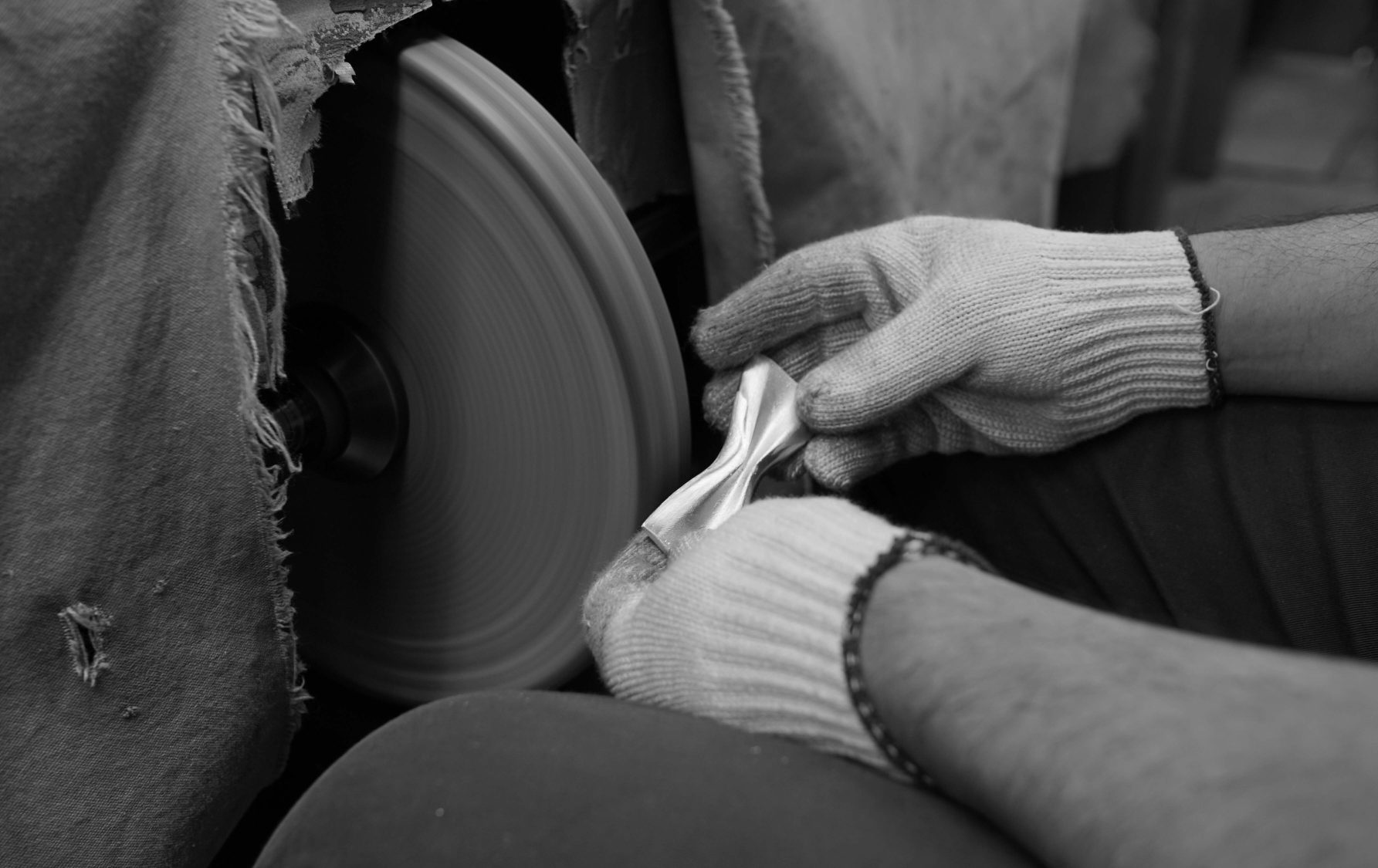
Lemnos Sustainability 02
Breathing Life into Metal Products – Lemnos’ Dedication to Craftsmanship
Many of Lemnos’ products are made of metal. The manufacturing process is carried out in collaboration with partner factories located in various regions, such as Toyama and Niigata, depending on the type of metal and method of processing.
This article highlights one such partnership with a group company known as Takata Factory. Takata Factory specializes in the casting and finishing of non-ferrous metals, including copper and aluminum alloys. Casting involves pouring molten metal into sand molds that have cavities in the shape of the desired product. Sand molds are made by compacting specially formulated sand designed for casting. The type and composition of the sand vary from factory to factory, reflecting each facility’s unique characteristics.
The process of compacting a sand mold
There are two primary methods for forming relatively thick metal products. One method involves machining the product from a solid metal block, while the other uses casting by pouring molten metal into molds. Each method is better suited to certain products, depending on the shape. For example, when producing a bowl-shaped item, machining from a solid block requires excessive cutting time and results in some material being wasted. On the other hand, casting minimizes the need for cutting, reduces the overall processing time, and prevents material wastage. In theory, casting appears ideal, but in practice, it demands advanced techniques and expertise to avoid defects such as sand inclusions or tiny air pockets that can form during pouring. Compared to machining, casting requires higher skill levels and know-how.
A pattern for forming sand molds. The channels attached around the disk are known as gates, and their placement requires technical expertise. After casting, the products undergo finishing processes, such as coloring, to complete their final appearance.
Product: Quaint/green (AZ15-06 GN)
The process of pouring molten brass into the sand mold
A clock made by casting bronze alloys. These clocks are left uncolored, allowing users to fully appreciate the natural texture and character of the metal.
Product: HALO/bronze (MK19-05 BZ)
Many of the metal products manufactured by Takata Factory are left uncoated. This is not only to allow users to enjoy the natural texture of the metal, but also to encourage long-term use through refinishing and polishing.
Why does Takata Factory put so much emphasis on polishing? Since its founding, the company has been producing Buddhist altar fittings for the Jodo Shinshu Otani-ha sect, which are known for their mirror-polished surfaces that are left uncoated to reveal the raw metal. Inspired by this tradition, Takata Factory continues to create uncoated products. However, uncoated metals are prone to oxidation and other chemical reactions, which can cause surface tarnishing. For Buddhist altar fittings, tarnished surfaces are polished back to their original state. This process can be repeated over generations, allowing the items to be used for a long time. Drawing from this experience, Lemnos offers refinishing services for products like ice cream spoons, so these items can be cherished and used for many years.
Using simple tools like buffs, skilled artisans polish each product by hand.
Before and after of refinishing. Many customers request polishing services for products with white rust or scratches.
Product: 15.0% ice cream spoon/No.01 vanilla (JT11G-11)
While modern methods, such as chemical-based electrolytic polishing and automated barrel polishing, are available, Takata Factory polishes many of its products by hand. Skilled craftsmen use simple machines equipped with rotating buffing wheels made from felt or cotton, polishing each piece one by one with care. (The term “buff” comes from the English word for tanned animal hides, such as cow or deer skin, which were once used for polishing. Today, the term is still used to refer to polishing wheels.) Why does Takata Factory insist on hand-polishing? When polishing curved surfaces, artisans carefully feel the surface to maintain its shape. This level of precision can only be achieved through manual craftsmanship. Metal surfaces are harder than materials like wood, requiring significant force to polish. The polishing process demands a high level of both skill and concentration, as even a small lapse in attention can cause the product to forcibly fly off, potentially leading to serious injury.
Buddhist altar fittings for the Jodo Shinshu Otani-ha sect. These items are carefully polished, even on the most intricately decorated parts.
The polishing process is akin to breathing life into solid metal blocks, much like how sculptors bring statues to life with their chisels. We hope you will take the time to experience Lemnos’ finely polished metal products, crafted using Takata Factory’s advanced casting techniques.
If your product becomes scratched or tarnished, please feel free to consult us for repair services.
Takata Factory: Polishing and Finishing Processes